Delivering safety in busy warehouses
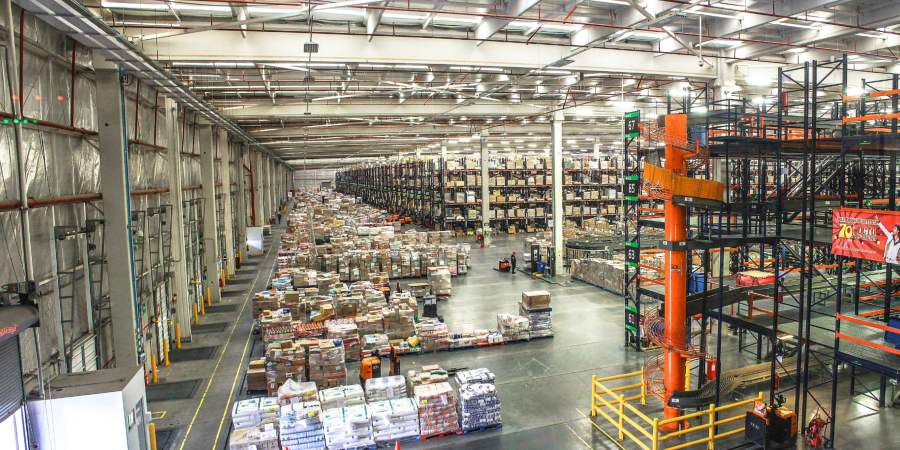
In recent years, companies with high-hazard work environments have made great strides in improving the safety conditions of their workplaces. But in most of the cases, hazards come into light when an incident occurs – although there are plans and procedures in place that help an employee’s ability to detect hazards, improvement in safety performance and culture remains an on-going process.
Consider a hissing valve emitting gas, or a missing handrail on a platform, or a pool of oil on the floor – all of them are present plainly in sight and the hazards they represent are obvious. But in case of a sharp metal edge at a head height just behind, or a pressure gauge tipping past its operating limit, these can turn lethal, if no one notices or recognizes them.
Now ever since the pandemic has struck, warehouses are struggling with an excess of ‘undeliverable’ products that were ordered by companies that shut down to prevent the spread of COVID-19 pandemic.
In this extra busy time, it becomes important for the employers to keep their workers safe amidst all such on-going activities (backlog orders). A generative culture is essential, where safety observations are used quickly to make safe working through making modifications in workers’ behaviours and streamlining of procedures.
Review forklift and pedestrian safety procedures
As simple as this might sound, keeping people safe while they’re walking near moving equipment becomes crucial when there’s a lot of inventory that consumes space. (Stacks of products can create blind spots for people crossing paths)
In these tough times, there might be conditions where pedestrian aisle becomes a storage location or a forklift parking location. Any such risk areas need to be evaluated – complacency must be addressed and resolved.
Proper virtual training that emphasizes on making workers understand the importance of practices and procedures goes a long way in these tough times – especially when new people are added into the mix.
Besides, a McKinsey report presents a new approach to oil and gas companies for safety awareness. This combines training with assessment – it uses VR tools to expose users to a realistic but hazard-laden environment. ‘Real reality’ environments find it difficult to assess the capabilities of a large number of workers in a short time, hence VR shrinks the gap between talking about safety and getting personally involved.
Ensure safe loading/unloading of trucks
Any process in place that confirms whether a truck trailer is safe for loading/unloading is necessary. Ideally, a truck must be securely attached to the loading bay via a ‘dock-lock’ – a hook from the bottom of the trailer that attaches to the dock.
When the work in a workplace increases, it is likely (especially in warehouses) that forklifts may fall into the gap between truck and loading bay, leading to fatal consequences. Busy people may affect work and loading/unloading safety is one of the systems that could possibly get disturbed.
Even the stacking of products in ways that make them unstable should be thoroughly checked – depending upon the weight and characteristics of the products, one can get trapped in for quite some time until people gather the right equipment and resources to remove the collapsed product.
Focussing on simple ways can observe the worker performance more precisely and the results can generate a real impact on performance, providing an edge in an ever-more complex warehousing landscape.
Thanks for sharing the great information on warehouse safety.Your warehouse holds not only your stock but also lots of hazards. It’s important to know the dangers that come with using forklifts on loading Stocks in warehouses. ! Here is a list of warehouse safety